I've acquired some Aramid fiber aka kevlar which is used for strength in optic fibre patch cords, not exactly food grade but still.
When it unravels its such a bugger that usually its best to throw away, hence me plaiting and taping it.
Theres no jelly or silicone coating on the fibers, I was thinking a steam or boil to clean before using for a wick.
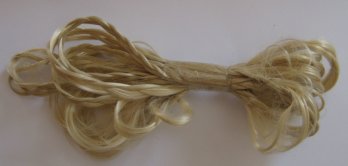
Heres some info I found from a fire twirling site, Home of POI
Whats your thoughts on the matter?
Maybe only in a temp control mod?
When it unravels its such a bugger that usually its best to throw away, hence me plaiting and taping it.
Theres no jelly or silicone coating on the fibers, I was thinking a steam or boil to clean before using for a wick.
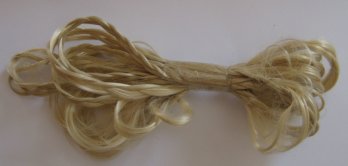
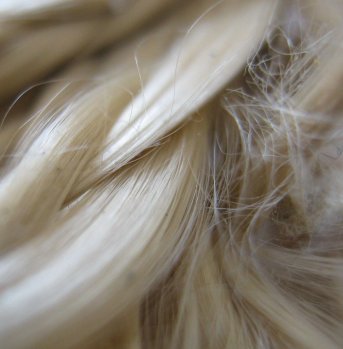
Heres some info I found from a fire twirling site, Home of POI
100% KEVLAR ® or 100% Aramid
100% KEVLAR ® or 100% Aramid would definitely be the most expensive form to make a wick out of. Most shops put "KEVLAR Wick" and omit everything else in the weave.
FOR
AGAINST
- Sounds good ie "I am using professional 100% KEVLAR ® wicks"
- In the correct weave they are very absorbent.
- Soaks in fuel well.
- Excellent capillary flow of fuel to the flame.
- Reasonable abrasion resistance, although much less than wire inserted or fiberglass.
- Excellent heat insulator
- Great for towing cars???
- Looks like really good superior and solid wick at the start
- Kevlar degenerates at 650 degrees Fahrenheit (343 degrees Celcius).
Tips and notes
- Weave will fall apart and wear quicker than Wicks woven with metal strands or fiberglass.
- KEVLAR ® begins to disappear at 427degree Celsius (800 degree Fahrenheit). turns into a gas.
- KEVLAR ® and Aramids degrade slowly when under daylight (UV).
See also What is KEVLAR ®?, How to make your wick last longer?, Fire head construction, All about metal parts used in fire twirling equipment
- Nomex degenerates at 450 degrees Fahrenheit (232 degrees Celcius)
- Fire may get to about 800 degrees Fahrenheit (426 degrees Celcius) however under the flame it will be much cooler.
- Some weaves have metal thread in it to provide rigidity to the weave. Not recommended for eating with because of the very hot metal fibres.
- PVA, Elmers or white school glue can be used on the edges of all these wicks to provide enhanced abrasive resistance. The heat will harden and cure the glue.
- Wrap KEVLAR ® blend wicking over cotton wick. Fuel from Cotton will feed into the Kevlar ® blend where it will be burnt.
- There are many manufacturers of these products around the world. Differing weaves and mixtures of the materials making up the weave can affect soakability, wear and tear, abrasive and burning characteristics. So these factors should also be considered. Just because one is cheaper does not mean it will be cheaper in the long term. Also one blend may be weaved to produce different characteristics of another wick of the same blend. What you use will most probably come down to where you are, how long you need it to last, what you want to spend and what is readily available.
References KEVLAR® technical guide, Silica Glass Fibres, KEVLAR® Para-Aramids - NOMEX®
Use of the KEVLAR ® brand in any printed brochures, catalogues, packaging, exhibition mediums, websites, Internet pages, or any other materials is not permitted without a license from DuPont.
"What to use as wick?" was first uploaded by HOP and has been viewed 68254 times.
Whats your thoughts on the matter?
Maybe only in a temp control mod?