Basically it starts with a furnace, mine I built some years ago as my son wanted one.
Buying a bag of refractory cement and using buckets as the form is the cheapest way to go. Some youtubers use those white insulation bricks that can be cut with a wood saw, but at R900 for 10 its gonna be an expensive build.
Im using a diaphragm pump and gravity drip car oil, so the brass valve with the red handle is a way of regulating the air and the large flow control hospital drip thingy is for controlling the oil drips. Its just bent aluminium with a nylon wheel on a SS shaft.
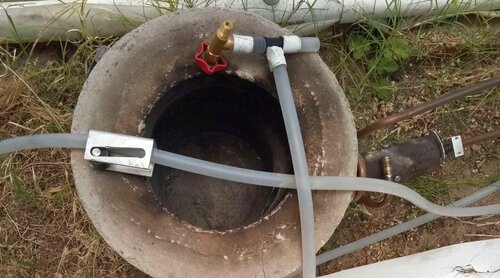
My main mission was finding a source for the molding sand(greensand), no success so I made my own.
AFS75 grade2 is the finest sand from Cape silica in Blackheath. (R204 for 40kg)
Eccabond N is bentonite powder from Serina Trading out Noordhoek way but collected in Bellville south. (R285 for 25kg)
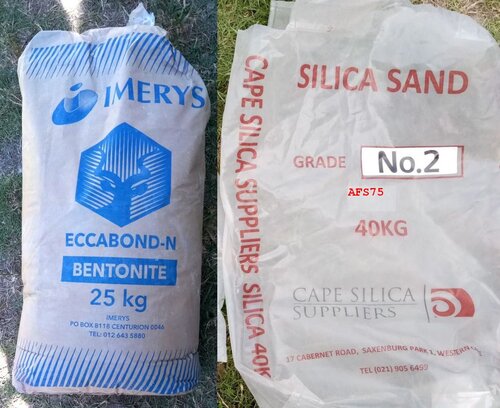
The sand must be mixed with 7 to 10% clay or 7:1 by volume. I used a big paint stirrer (120mmx600mm) but my drill got rather hot, not knowing which one would be best, I bought all 3 types Brights hardware had, turned out the small 80x400 one worked best. (R104)
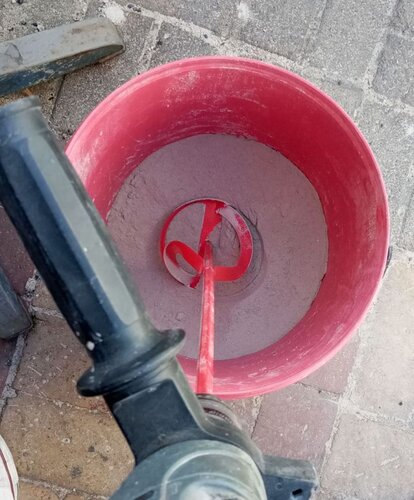
Some of the large tools I have sourced and made. The length of 6m rebar was R85 and I've used 4m so far for the 3 crucible tools on the right.
Salamander A4 crucible from https://www.gjsupplies.co.za/crucibles.html (R405)
Sieves are, 0.5mm at the top, its the large one from Makro, Chef's Kitchen 2-Pack Strainer (R129)
The red handle is a 1.6mm and the flat disk is a 1mm from Chinatown.
The paint stirrers from Brights, big is R145, small on on the right is R104 and the thingy in the middle is a H/Duty grout mixer at R79.95.
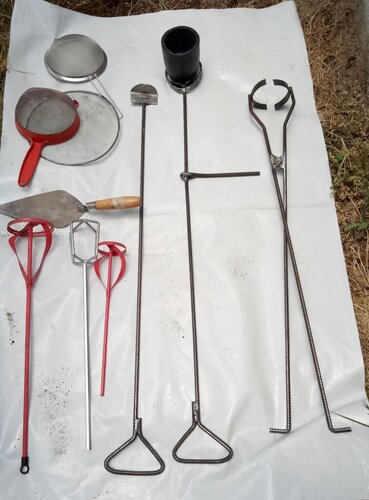
The small items are, parting powder bag I sewed myself, builders lime from Penny pinchers (R86 for 25kg)
Rubber mallet I've had for 10 years, was going to do wooden flooring but changed my mind.
Dunno what the tongs were for but they were in my dad's tools.
The small trowel (R39.50 ) and brushes were from PNA.
The wood sprue's, riser and sand rammer were made on the lathe, the tuning fork thingy I also welded up from some rebar.
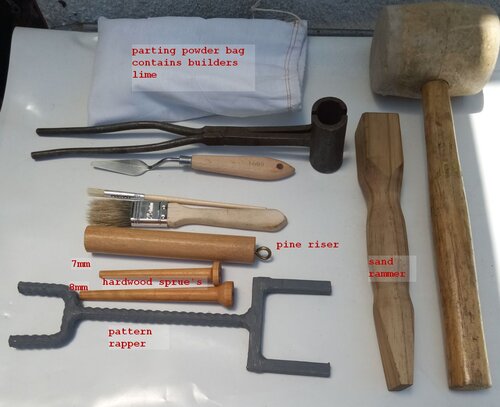
The most difficult part so far has been getting the water amount in the greensand just right.
I use a knapsack sprayer from Brights (on special at R299 till 20 Dec 2020), its easy to use , works well and IMO is the last word in hand sprayers.
I had my sand too wet so its been drying in the sun for the last 2 days, rake and check, turn and dry.
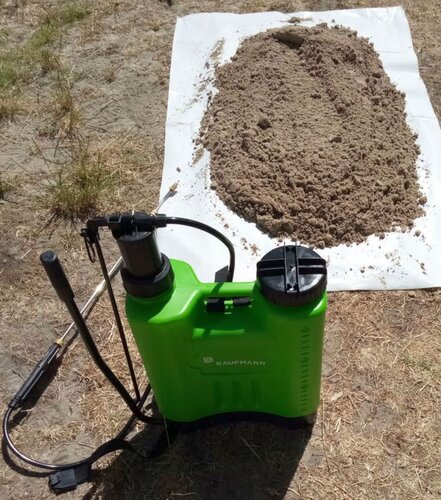
A lot of Ytubers suggest the hand squeeze test, but its not always an accurate test.
One of the tubers I sub has been in the foundry business for the last 50 years and is my first stop for foundry related research, Olfoundryman at https://www.youtube.com/channel/UC90RoN_IjSRF18jAG0HIA6g.
His method involves rubbing the sand through a sieve and seeing how it falls.
My sand had a clean break but was still too wet to go through the sieve with the 1mm openings.
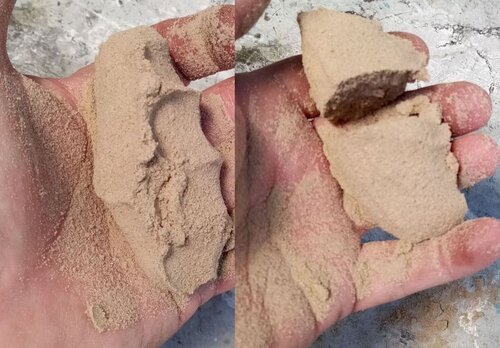
Some views of sieved sand, top pile is from the middle of my 40kg barrel, surface level is the bottom pile.
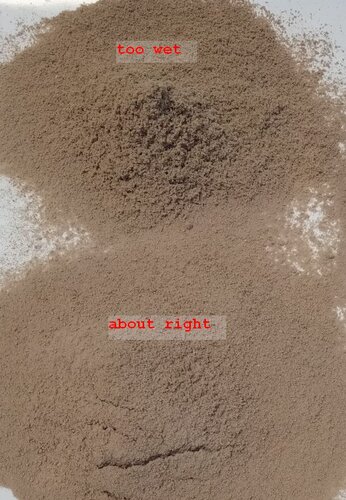
When the sand is too wet, it sticks where it falls giving the appearance of holes in a spiky pile.
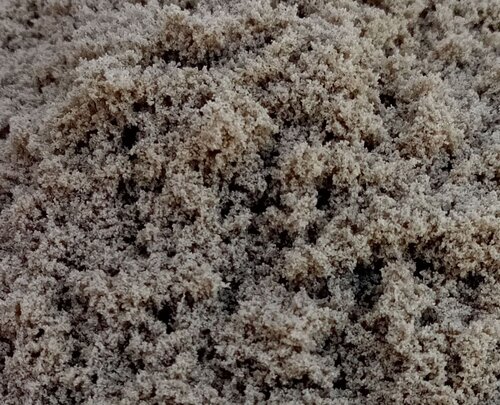
Finally at the end of the day I'm getting close.
Still difficult to push it through the sieve but the pile is much smoother and the holes much smaller.
I decided to empty my 50 L sand bin and put the drier top sand on the bottom and the wetter bottom sand on the top and let it overnight.
If things look good in the morning the next episode will be ramming up a molding flask.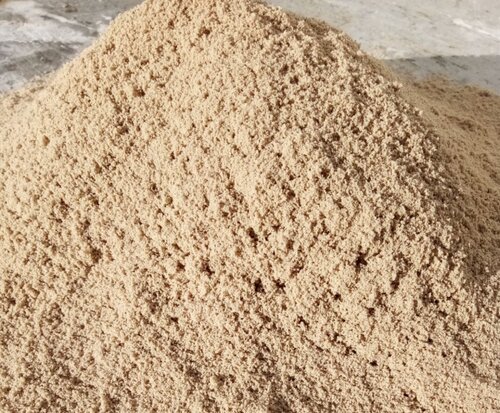
Before anyone suggests my crucible pourer is kak and the crucible is going to fall out...
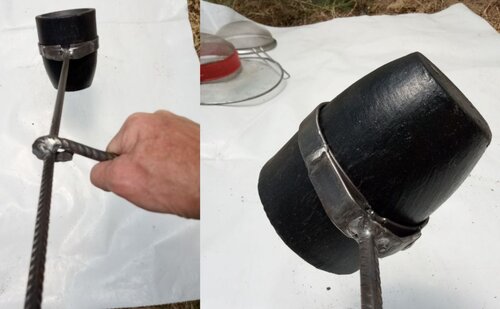
uh uhhh, not today.
Whats it cost?
So far R1636 not including the unnecessary large paint stirrer and grout mixer.
Buying a bag of refractory cement and using buckets as the form is the cheapest way to go. Some youtubers use those white insulation bricks that can be cut with a wood saw, but at R900 for 10 its gonna be an expensive build.
Im using a diaphragm pump and gravity drip car oil, so the brass valve with the red handle is a way of regulating the air and the large flow control hospital drip thingy is for controlling the oil drips. Its just bent aluminium with a nylon wheel on a SS shaft.
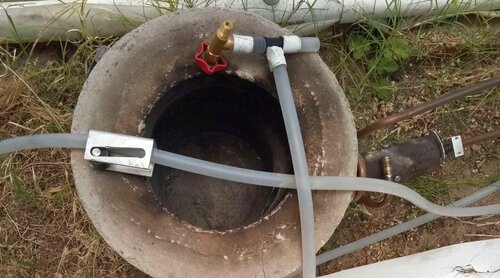
My main mission was finding a source for the molding sand(greensand), no success so I made my own.
AFS75 grade2 is the finest sand from Cape silica in Blackheath. (R204 for 40kg)
Eccabond N is bentonite powder from Serina Trading out Noordhoek way but collected in Bellville south. (R285 for 25kg)
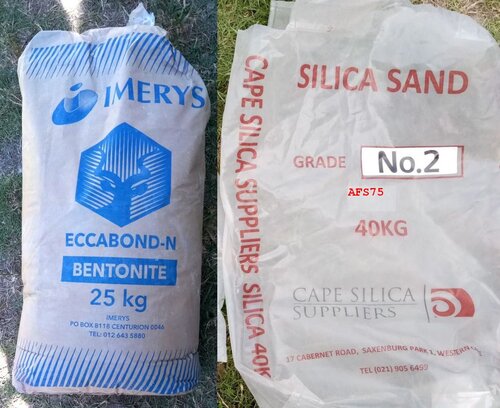
The sand must be mixed with 7 to 10% clay or 7:1 by volume. I used a big paint stirrer (120mmx600mm) but my drill got rather hot, not knowing which one would be best, I bought all 3 types Brights hardware had, turned out the small 80x400 one worked best. (R104)
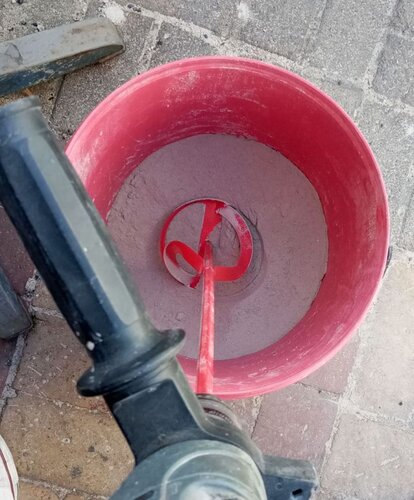
Some of the large tools I have sourced and made. The length of 6m rebar was R85 and I've used 4m so far for the 3 crucible tools on the right.
Salamander A4 crucible from https://www.gjsupplies.co.za/crucibles.html (R405)
Sieves are, 0.5mm at the top, its the large one from Makro, Chef's Kitchen 2-Pack Strainer (R129)
The red handle is a 1.6mm and the flat disk is a 1mm from Chinatown.
The paint stirrers from Brights, big is R145, small on on the right is R104 and the thingy in the middle is a H/Duty grout mixer at R79.95.
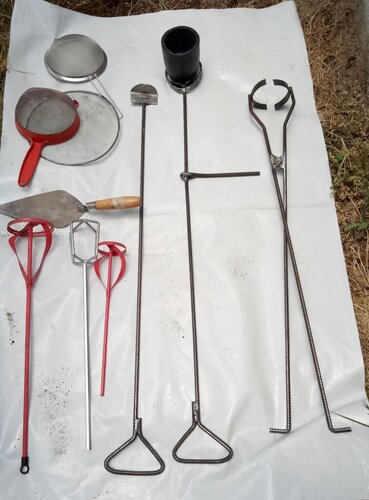
The small items are, parting powder bag I sewed myself, builders lime from Penny pinchers (R86 for 25kg)
Rubber mallet I've had for 10 years, was going to do wooden flooring but changed my mind.
Dunno what the tongs were for but they were in my dad's tools.
The small trowel (R39.50 ) and brushes were from PNA.
The wood sprue's, riser and sand rammer were made on the lathe, the tuning fork thingy I also welded up from some rebar.
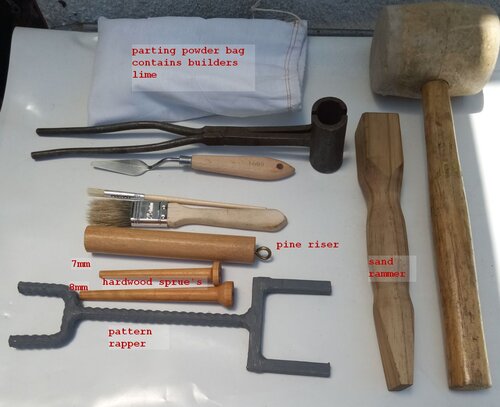
The most difficult part so far has been getting the water amount in the greensand just right.
I use a knapsack sprayer from Brights (on special at R299 till 20 Dec 2020), its easy to use , works well and IMO is the last word in hand sprayers.
I had my sand too wet so its been drying in the sun for the last 2 days, rake and check, turn and dry.
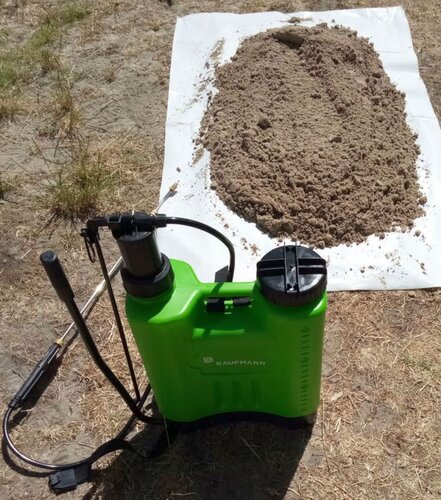
A lot of Ytubers suggest the hand squeeze test, but its not always an accurate test.
One of the tubers I sub has been in the foundry business for the last 50 years and is my first stop for foundry related research, Olfoundryman at https://www.youtube.com/channel/UC90RoN_IjSRF18jAG0HIA6g.
His method involves rubbing the sand through a sieve and seeing how it falls.
My sand had a clean break but was still too wet to go through the sieve with the 1mm openings.
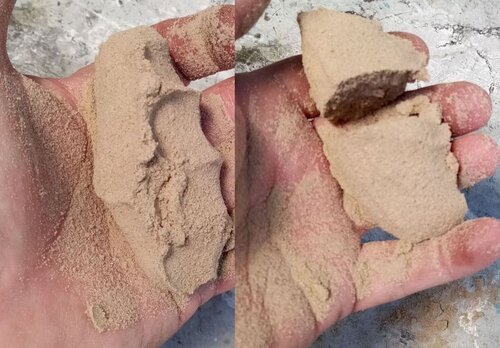
Some views of sieved sand, top pile is from the middle of my 40kg barrel, surface level is the bottom pile.
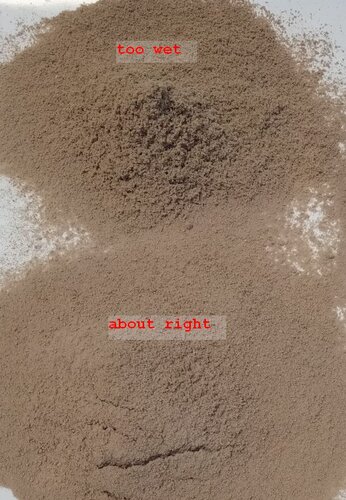
When the sand is too wet, it sticks where it falls giving the appearance of holes in a spiky pile.
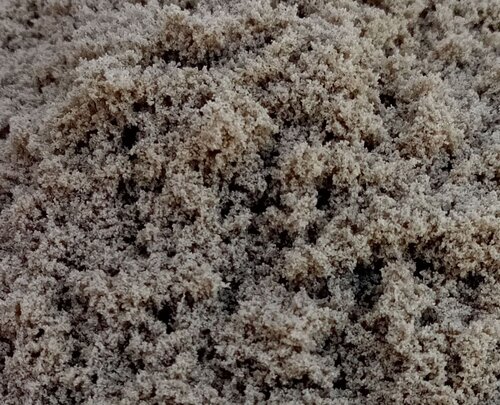
Finally at the end of the day I'm getting close.
Still difficult to push it through the sieve but the pile is much smoother and the holes much smaller.
I decided to empty my 50 L sand bin and put the drier top sand on the bottom and the wetter bottom sand on the top and let it overnight.
If things look good in the morning the next episode will be ramming up a molding flask.
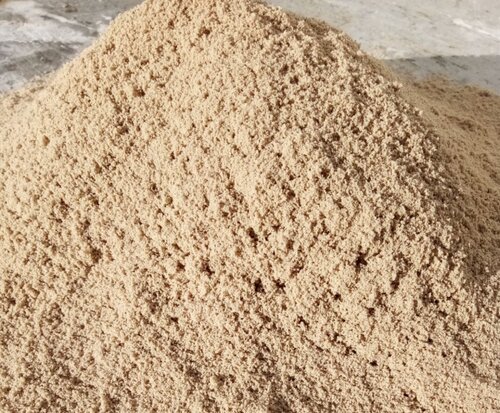
Before anyone suggests my crucible pourer is kak and the crucible is going to fall out...
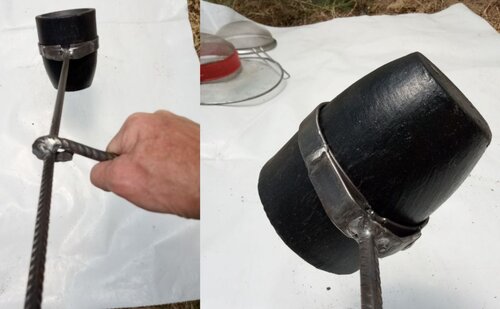
uh uhhh, not today.
Whats it cost?
So far R1636 not including the unnecessary large paint stirrer and grout mixer.